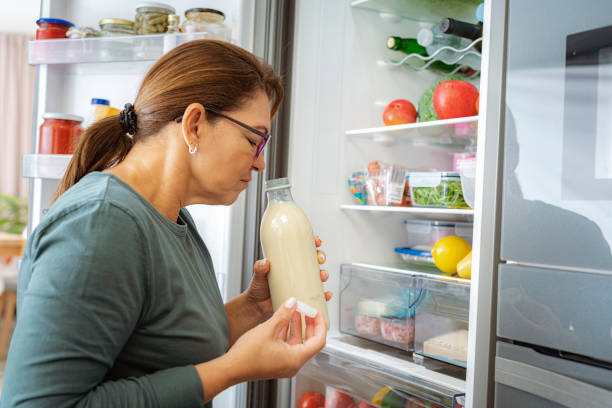
You know the feeling. That little pause, the slight dread before you swing open the refrigerator door, hoping the light comes on and the air feels crisp. But today? Not so much. Maybe things are just slightly off, or perhaps the cooling has stopped altogether. When this happens, it might be time to consider a sealed system repair — one of those household hiccups that throws your whole day off track.
Sometimes, getting your appliance back on track is straightforward. But other times, that lack of chill points to deeper system problems, hinting at trouble within what technicians call the “sealed system.” This isn’t your everyday appliance repair task; it involves the very heart of how your fridge or freezer makes things cold.
Dealing with a potential sealed system issue can feel daunting, mostly because it is complex. This kind of sealed system work requires specific tools, training, and a careful hand.
Here at S.T.A.R. Appliance Repair, we get it. We see these intricate issues often, and we know how crucial reliable refrigeration is, especially here in California. Our aim isn’t just to fix things, but to help you understand what’s going on inside your appliance. So, let’s gently pull back the curtain on sealed systems: what they are, what goes wrong, and why their repair is truly a specialized craft.
So, What Exactly Is This “Sealed System”?
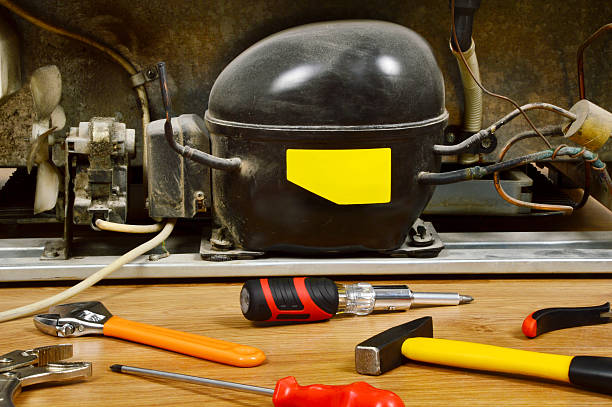
Imagine a tiny, self-contained highway system tucked away inside your appliance. That’s basically the sealed system – a continuous, completely closed loop of tubing. It’s sealed for a reason: it holds a special fluid, the refrigerant, which needs to stay pure and contained to do its job.
And what’s its job? Simple: cooling. The whole point of this intricate setup is to perform a little magic trick – moving heat from inside your fridge or freezer to the air outside it. This constant heat exchange is what keeps your groceries fresh and your ice cream frozen. If something goes wrong, though, you may need a sealed system repair to restore the cooling performance and prevent spoilage.
This process isn’t handled by just one part, but a team working in perfect sync:
-
- The compressor: Think of this as the engine or the heart of the system. It pumps the refrigerant gas along its route, squeezing it and making it hot. You often hear its low hum when the fridge is running.
-
- The condenser coils (and condenser): Usually found on the back or underneath, these coils are where the hot, high-pressure refrigerant releases the heat it picked up inside. It cools down and turns from a gas back into a liquid here. If you’ve ever felt warmth coming off the back of your fridge, that’s the condenser doing its thing.
-
- The capillary tube (or expansion valve): This is a super-narrow section of the tubing. As the liquid refrigerant is forced through this tight spot, its pressure drops dramatically, making it instantly very cold – like the spray from an aerosol can.
-
- The evaporator coils (and evaporator): Located inside the freezer or fridge compartment, these coils are where the magic really happens. The now super-cold refrigerant flows through them, absorbing heat from the air inside. This absorption process makes the refrigerant boil back into a gas, leaving the inside of your appliance wonderfully chilled. That frosty panel at the back of your freezer? That’s often the evaporator.
The refrigerant itself is carefully chosen for its ability to change between liquid and gas states at just the right temperatures. It just cycles round and round – getting squeezed, releasing heat, getting cold, absorbing heat – endlessly keeping things cool. It’s a clever bit of engineering hidden just behind the door, and when something goes wrong, sealed system repair is often required to restore proper function.
Common Sealed System Issues
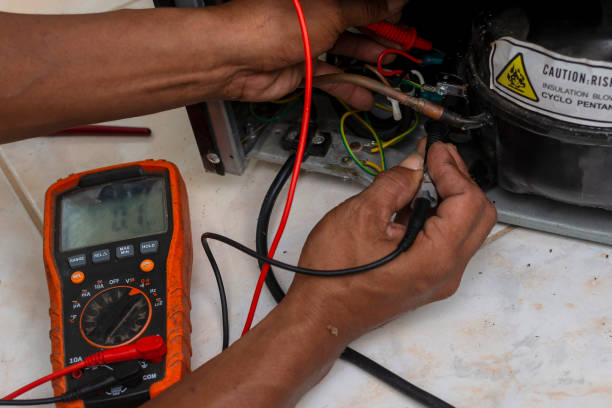
Even the best-engineered systems can hit a snag, and that hard-working sealed system in your fridge or freezer is no exception. Because it’s a pressurized, constantly running closed loop, certain system problems tend to be the usual suspects when deep cooling troubles arise. Think of these not as minor glitches, but often as significant issues needing expert attention – a true sealed system issue that may require professional sealed system repair to restore proper function.
Here are some of the common culprits:
-
- The dreaded refrigerant leak: This is probably the most frequent offender. Tiny vibrations, age, or even a microscopic flaw can cause the system to spring a leak. As the essential refrigerant gas escapes, the cooling ability gradually fades, sometimes until it’s gone completely. You might notice the compressor seems to run all the time, trying in vain to cool things down.
-
- Compressor burnout: If the compressor is the heart, sometimes that heart just gets tired and gives out. This can happen due to simple wear and tear over years of service, electrical problems, or sometimes as a consequence of running too hard because of another issue (like a refrigerant leak). Symptoms can range from the appliance being completely silent and warm, to ominous clicking or humming sounds followed by silence.
-
- Clogs and restrictions: Imagine a traffic jam inside those narrow tubes. Contaminants like tiny particles or, more critically, moisture, can create blockages, often in the super-thin capillary tube or filter-drier component. This disrupts the flow of refrigerant, leading to inefficient cooling, strange frost patterns perhaps only on part of the evaporator coils, or the compressor laboring under strain.
-
- Internal contamination: Moisture is the arch-enemy of a sealed system. If it gets inside (perhaps during a previous improper repair attempt), it can react with the refrigerant and oils, creating sludge and acids that cause internal corrosion, blockages, and ultimately, lead to further damage and component failure.
Any of these issues effectively stops your appliance from doing its one crucial job: keeping things cold.
What Does Sealed System Repair Actually Involve?
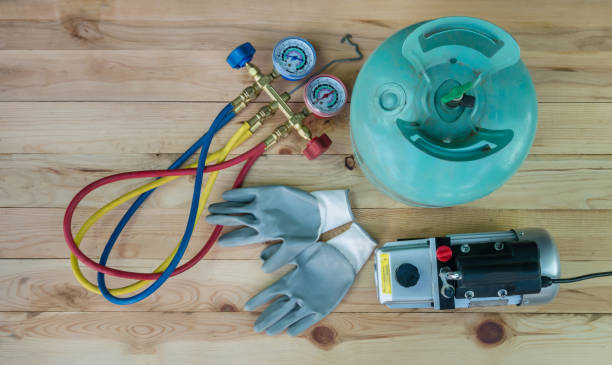
So, you’ve got symptoms pointing towards a sealed system issue. What does getting it fixed look like? Forget quick fixes or simple part swaps; sealed system repair is more like delicate surgery for your appliance. It demands patience, precision, and the right expertise.
Before any “operating” begins, the absolute first step is diagnosis. A qualified technician – like the certified pros at S.T.A.R. Appliance Repair – needs to thoroughly investigate. They’ll use specialized tools and knowledge to confirm if the problem truly lies within the sealed system or if it’s something else playing tricks. Guesswork has no place here.
Once a sealed system fault is confirmed, the actual sealed system repair process generally follows these careful steps:
-
- Gaining access: First, the technician needs to reach the system’s components, which often involves carefully moving the appliance and removing panels or parts to expose the tubing, compressor, and coils.
-
- Handling the refrigerant (the critical part): This isn’t optional. Before the system can be opened, any remaining refrigerant gas must be safely recovered using specialized EPA-approved equipment. It absolutely cannot just be released into the air – it’s harmful and illegal.
-
- Making the repair: This is where the core fix happens. It could involve:
-
- Finding the exact location of a leak (sometimes using UV dye or electronic sniffers) and meticulously repairing it, often by brazing (a type of high-temperature soldering).
-
- Replacing a failed component entirely, such as installing a new compressor, evaporator, condenser, or filter drier. Sometimes the capillary tube needs replacing if it’s blocked beyond cleaning. Cleaning condenser coils or evaporator coils might also be part of the job.
-
- Making the repair: This is where the core fix happens. It could involve:
-
- Preparing for new refrigerant (evacuation): After the repair, the system is wide open to contamination. Air and especially moisture are now inside, and they must be removed. A powerful vacuum pump is connected to pull out practically every trace of air and moisture. Skipping or rushing this step is a recipe for further damage and the repair failing prematurely.
-
- The precise refill (recharging): With the system clean, dry, and sealed again, it’s time to recharge it with new refrigerant. This isn’t like filling a gas tank; the technician uses precise gauges and scales to add the exact type and amount of refrigerant specified for your appliance. Too much or too little, and it won’t cool correctly.
-
- Testing, testing, testing: Finally, the appliance is turned back on, and the technician carefully monitors pressures and temperatures to ensure the cooling is restored and the system is operating smoothly and efficiently.
It’s a methodical, detailed process – far beyond typical handyman tasks.
Why Is Sealed System Repair Such a Specialty?
We’ve seen that sealed system work is pretty involved. But what makes it so different from other types of appliance repair? Why can’t the friendly neighborhood handyman, or even every appliance tech, necessarily handle it? It boils down to a few critical factors that set it apart significantly. Think of it this way: swapping a faulty ice maker is basic arithmetic; working on the sealed system is advanced calculus.
Here’s why it demands a specialist’s touch:
-
- It involves breaching the core system: Unlike fixing a door gasket or replacing a shelf, this repair means opening up that carefully balanced closed loop. This action alone requires specific procedures to do safely and correctly, preserving the integrity of the whole system.
-
- Highly specialized (and expensive) tools: Forget your standard wrench set. Sealed system repairs require gear like:
-
- Refrigerant recovery machines (to safely remove the old gas).
-
- High-vacuum pumps (to remove damaging air and moisture).
-
- Manifold gauge sets (to read system pressures accurately).
-
- Precision charging scales (to measure the new refrigerant exactly).
-
- Leak detectors (electronic “sniffers” or UV dye kits).
-
- Brazing equipment (for welding the copper tubing). This isn’t equipment most general repair services invest in or carry daily.
-
- Highly specialized (and expensive) tools: Forget your standard wrench set. Sealed system repairs require gear like:
-
- The refrigerant factor: safety and legality: This is a huge one. In the United States, technicians must be EPA Section 608 certified to handle refrigerant gas. This isn’t just red tape; refrigerant requires careful handling for safety (it can cause frostbite or displace oxygen in enclosed spaces) and environmental protection. Improper release is illegal and harmful. Certified techs know the protocols.
-
- Deep technical know-how: Understanding the physics of the refrigeration cycle – pressures, temperatures, phase changes of the refrigerant – is crucial. Diagnosing subtle system problems, interpreting gauge readings correctly, and knowing how different components interact requires specific training and experience beyond general mechanics.
-
- High risk of causing further damage: This is where good intentions can go wrong. Tiny mistakes during a sealed system repair, like introducing a bit of moisture, slightly under or overcharging the refrigerant, or making a weak brazed joint, can quickly lead to component failure (especially wrecking a brand new compressor!) and repeat breakdowns. This turns a fix attempt into much more expensive repairs down the line.
Simply put: don’t DIY this. The risks to your safety, your appliance, your wallet, and the environment are just too high.
This unique combination of required tools, mandatory certifications, in-depth knowledge, and the high stakes involved is why you need specialists. Technicians at S.T.A.R. Appliance Repair, for example, have the specific training, EPA certification, and equipment necessary to perform sealed system work correctly and safely.
Spotting a Potential Sealed System Issue
Sometimes your fridge or freezer practically shouts that something’s wrong (like when it stops cooling entirely). Other times, the clues are more subtle. Here are a few signs that might point towards trouble brewing in that hidden sealed system:
-
- The chill is gone (or going): The most obvious sign – food isn’t staying cold, or things in the freezer are getting soft.
-
- Running non-stop: You notice the compressor motor seems to be running constantly, but the inside temperature isn’t dropping. It’s working hard but going nowhere, possibly due to a refrigerant leak.
-
- Strange sounds: Instead of the usual gentle hum, you hear clicking, buzzing followed by silence, or other unusual noises from the compressor area.
-
- Oily spots: Finding greasy or oily residue near the compressor or coils could indicate escaping refrigerant carrying oil with it – a tell-tale sign of a leak.
-
- Weird frost patterns: Instead of an even frost, you see excessive frost building up only on a specific section of the evaporator coils inside.
Before you panic… check the simple stuff: It’s easy to jump to conclusions. Always quickly check if the thermostat setting got bumped, if the door seals are tight, if vents inside aren’t blocked by food items, and if the condenser coils (if accessible on your model, often at the back or bottom) are relatively clean and not caked in dust or pet hair.
But if you’ve checked the basics and the symptoms persist? That’s your cue. It’s time to stop guessing and call in a professional technician, like the certified experts at S.T.A.R. Appliance Repair, for an accurate diagnosis. They have the tools and know-how to determine if it’s truly a sealed system issue.
Why Trust S.T.A.R. for Your Sealed System Needs?
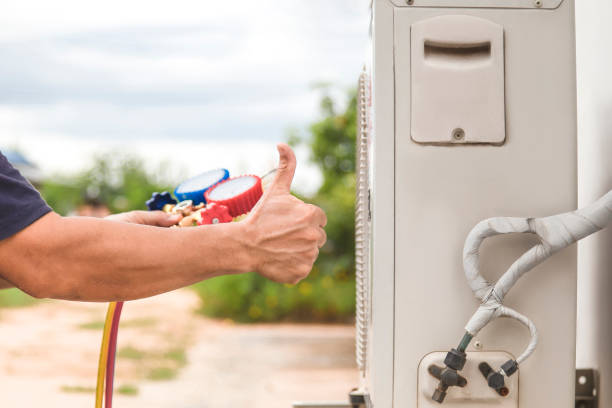
You get it now – sealed system work is definitely not a job for just anyone. It requires a specific skill set and equipment that goes beyond typical appliance repair. When the heart of your appliance’s cooling system is on the line, you want technicians who truly specialize in this delicate area.
Here’s what sets S.T.A.R. Appliance Repair apart:
Certified Expertise
Our technicians aren’t just generalists; they possess the necessary EPA certifications and have specific training and hands-on experience with sealed systems across various brands, including major names like Whirlpool.
The Right Tools for the Job
We invest in the specialized diagnostic, recovery, and repair equipment essential for performing sealed system work safely and effectively.
Focus on Quality Repairs
Our goal isn’t a quick patch-up. We aim to diagnose accurately and repair meticulously to prevent further damage and ensure your appliance runs reliably for the long haul.
Honest Assessments
We understand that sometimes expensive repairs might not be the most sensible option. We’ll give you a clear picture of the problem and the costs involved, helping you weigh your options between repair and replacement honestly.
And while we specialize in the complexities of refrigeration sealed systems, our expertise doesn’t stop there. We handle a wide range of other appliance repair needs too – from ovens and dishwashers to fixing that noisy dryer (which, by the way, involves completely different systems!).
Think you might have a sealed system issue? Don’t risk making things worse. For expert diagnosis and reliable refrigerator or freezer repair in California, give S.T.A.R. Appliance Repair a call. Reach out today – visit our website at homerepairs.pro or call us at (800) 915-6254.
Final Thoughts on Sealed Systems
So, that intricate network humming away inside your fridge or freezer – the sealed system – really is the star player when it comes to cooling. We’ve seen that issues like a sneaky refrigerant leak or a worn-out compressor aren’t minor bumps; they require careful, specialized sealed system repair.
Hopefully, it’s crystal clear now why this kind of work is in a league of its own. It demands specific tools, certified know-how for safely handling refrigerant gas, and a deep understanding to avoid causing further damage. It’s precision work, plain and simple.
Choosing a qualified, certified technician isn’t just about getting the job done; it’s about peace of mind and ensuring your appliance gets the expert care it needs. When facing potential sealed system problems, trust the pros with experience in sealed system repair. For reliable refrigerator repair or freezer service, remember S.T.A.R. Appliance Repair is here to help you keep things perfectly chilled.
Frequently Asked Questions
How do I know if my fridge needs sealed system repair?
Common signs include your fridge not cooling properly, the compressor running non-stop without chilling, strange noises near the compressor, oily spots indicating leaks, or uneven frost buildup inside the freezer. If basic checks don’t fix these issues, a sealed system repair may be necessary.
Why is sealed system repair more complicated than regular appliance repairs?
Sealed system repair is complex because it involves handling refrigerant in a closed, pressurized system. It requires specialized tools, EPA certification to handle refrigerants legally and safely, and technical know-how to diagnose and repair without causing further damage.
Can I attempt sealed system repair myself?
No. Sealed system repair is not a DIY task due to the risks involved with refrigerant handling, potential for causing further damage, and the need for specific tools and certifications. Always hire certified technicians for sealed system repair.
What does a typical sealed system repair process involve?
A sealed system repair includes diagnosing the problem, safely recovering refrigerant, locating and fixing leaks or replacing faulty components, evacuating moisture and air from the system, recharging with the correct refrigerant, and thoroughly testing to ensure the appliance cools properly again.
How much does sealed system repair usually cost?
The cost of sealed system repair depends on the exact issue, parts involved (like compressor replacement), and labor complexity. Since it is a specialized service requiring specific equipment and certification, prices can be higher than typical appliance repairs.
Why should I choose a professional service like S.T.A.R. Appliance Repair for sealed system repair?
S.T.A.R. Appliance Repair technicians are EPA certified and trained specifically for sealed system repair. We have the right tools and experience to safely and effectively diagnose and fix sealed system problems, ensuring long-lasting, quality repairs.
How long does sealed system repair take?
The duration varies based on the complexity of the issue but generally involves several hours. Precise diagnosis, careful handling of refrigerants, vacuuming out moisture, and testing all take time to ensure a successful sealed system repair.
Can sealed system repair prevent the need for a full appliance replacement?
Yes. Proper sealed system repair can extend the life of your refrigerator or freezer by fixing core cooling problems. However, if the damage is extensive or repair costs are too high, replacement might be a more cost-effective option.
What are the risks of delaying sealed system repair?
Delaying sealed system repair can cause the compressor to overwork and eventually fail, increase energy consumption, and risk spoilage of food inside. It can also lead to more expensive repairs or irreversible damage to your appliance.